Electric technologies, the future of the medical profession
The purchase of an injection mould represents an investment for a company, and throughout the year it also has to cover the associated running costs. But what if there were electrical moulding solutions available today using high technology? ERMO, a recognised expert in the design and manufacture of injection moulds, has broken new ground in this area, becoming a pioneer in the creation of durable moulds with high-performance cycle times. Find out more below.
The medical sector needs high-precision moulds for a wide range of technical parts used in medical devices, including syringe shields, mouthpieces, inhalers and nasal applicators. ERMO, a specialist in high-precision injection moulds since 1979, has the expertise to meet these needs. By designing electric moulds combined with major technologies such as E-IMA (In Mould Assembly 100% electric) or E-IMC (In Mould Closing 100% electric), ERMO enables companies to better control their process and the quality of the injected parts.
Stéphane Grossnickel, ERMO's Sales Director, underlines the company's commitment to the medical sector, pointing to its cleanroom production capacity. In the medical sector, ERMO's moulds, even small ones, often feature numerous cavities (up to 96 cavities), and the company is increasingly called upon for this type of project.
Since 2019, ERMO has experienced continued growth in the medical field, with international ambitions thanks to a new office in India and Mexico. In addition, with the recent integration of ERPA, which specialises in automation and robotisation, ERMO not only offers moulds, but also a complete solution incorporating peripherals connected to the press.
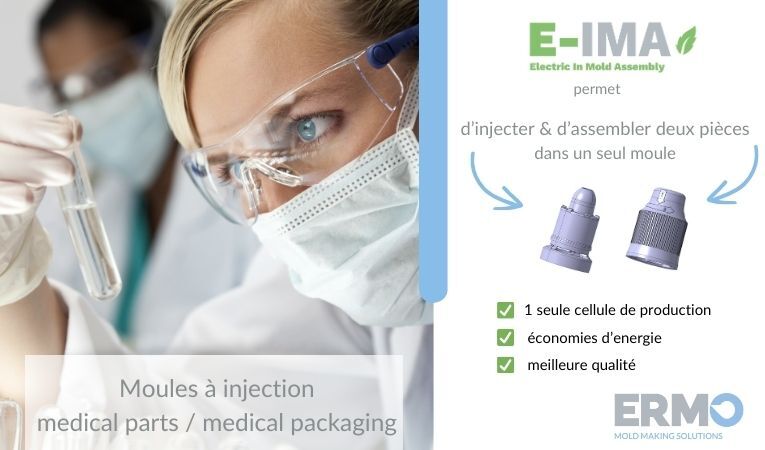
World Premiere E-IMA
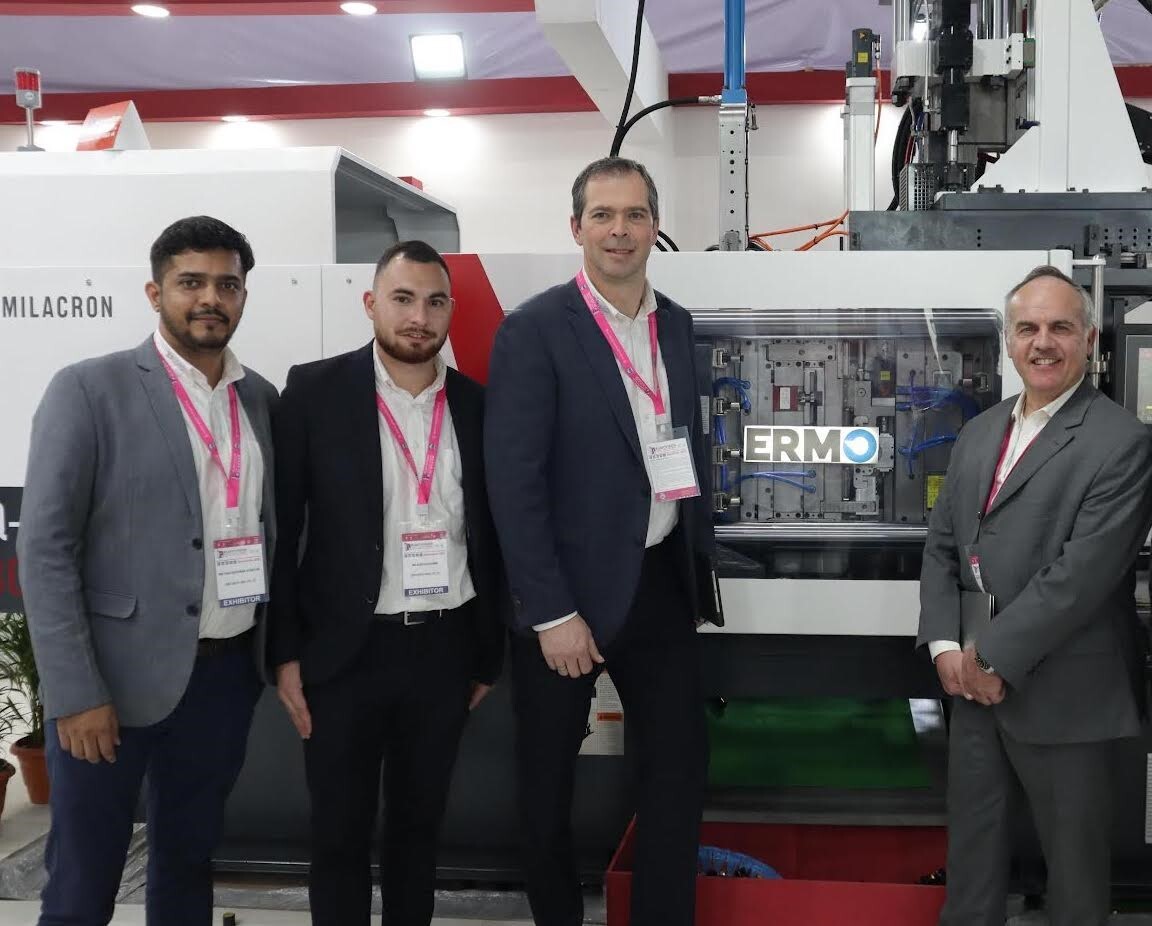
Our electrical assembly solution was presented for the very first time at the Plastivision trade fair, held in Mumbai from 7 to 11 December. Called E-IMA, this innovation enables two parts to be injected and assembled simultaneously on a single side of the mould. It gives us greater control over the assembly process and a 10% increase in productivity compared with the previous hydropneumatic version.
Next step : meet the ERMO team at Pharmapack in Paris 2024, stand C21, Hall 7.